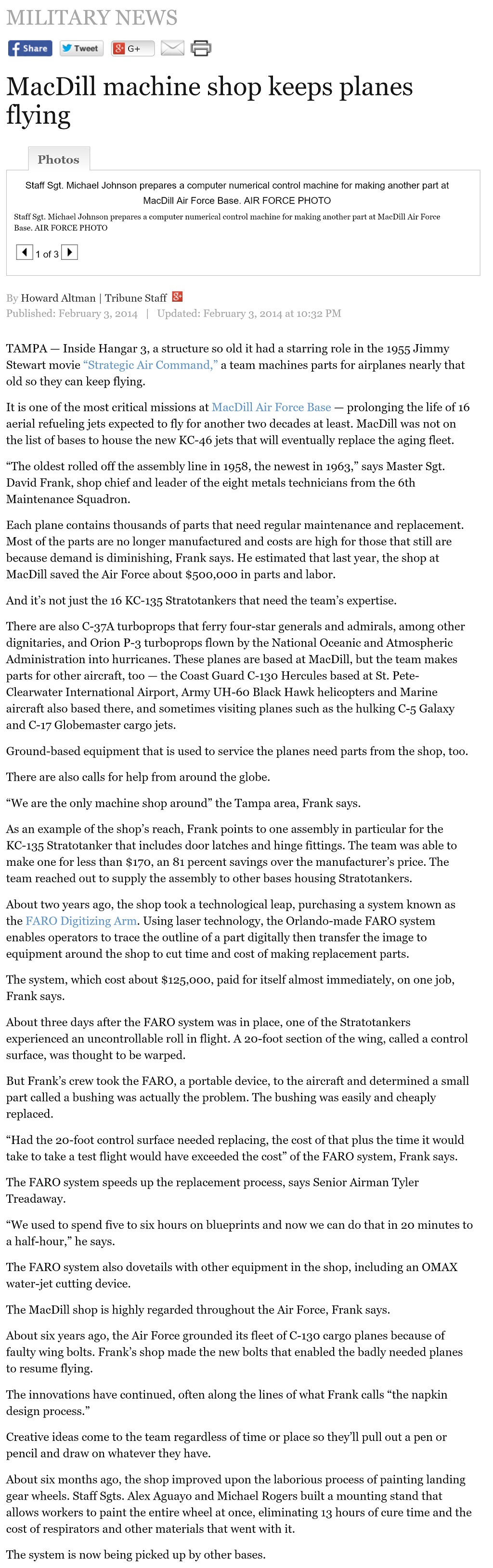
TAMPA — Inside Hangar 3, a structure so old it had a starring role in the 1955 Jimmy Stewart movie “Strategic Air Command,” a team machines parts for airplanes nearly that old so they can keep flying.
It is one of the most critical missions at MacDill Air Force Base — prolonging the life of 16 aerial refueling jets expected to fly for another two decades at least. MacDill was not on the list of bases to house the new KC-46 jets that will eventually replace the aging fleet.
“The oldest rolled off the assembly line in 1958, the newest in 1963,” says Master Sgt. David Frank, shop chief and leader of the eight metals technicians from the 6th Maintenance Squadron.
Each plane contains thousands of parts that need regular maintenance and replacement. Most of the parts are no longer manufactured and costs are high for those that still are because demand is diminishing, Frank says. He estimated that last year, the shop at MacDill saved the Air Force about $500,000 in parts and labor.
And it’s not just the 16 KC-135 Stratotankers that need the team’s expertise.
There are also C-37A turboprops that ferry four-star generals and admirals, among other dignitaries, and Orion P-3 turboprops flown by the National Oceanic and Atmospheric Administration into hurricanes. These planes are based at MacDill, but the team makes parts for other aircraft, too — the Coast Guard C-130 Hercules based at St. Pete-Clearwater International Airport, Army UH-60 Black Hawk helicopters and Marine aircraft also based there, and sometimes visiting planes such as the hulking C-5 Galaxy and C-17 Globemaster cargo jets.
Ground-based equipment that is used to service the planes need parts from the shop, too.
There are also calls for help from around the globe.
“We are the only machine shop around” the Tampa area, Frank says.
As an example of the shop’s reach, Frank points to one assembly in particular for the KC-135 Stratotanker that includes door latches and hinge fittings. The team was able to make one for less than $170, an 81 percent savings over the manufacturer’s price. The team reached out to supply the assembly to other bases housing Stratotankers.
About two years ago, the shop took a technological leap, purchasing a system known as the FARO Digitizing Arm. Using laser technology, the Orlando-made FARO system enables operators to trace the outline of a part digitally then transfer the image to equipment around the shop to cut time and cost of making replacement parts.
The system, which cost about $125,000, paid for itself almost immediately, on one job, Frank says.
About three days after the FARO system was in place, one of the Stratotankers experienced an uncontrollable roll in flight. A 20-foot section of the wing, called a control surface, was thought to be warped.
But Frank’s crew took the FARO, a portable device, to the aircraft and determined a small part called a bushing was actually the problem. The bushing was easily and cheaply replaced.
“Had the 20-foot control surface needed replacing, the cost of that plus the time it would take to take a test flight would have exceeded the cost” of the FARO system, Frank says.
The FARO system speeds up the replacement process, says Senior Airman Tyler Treadaway.
“We used to spend five to six hours on blueprints and now we can do that in 20 minutes to a half-hour,” he says.
The FARO system also dovetails with other equipment in the shop, including an OMAX water-jet cutting device.
The MacDill shop is highly regarded throughout the Air Force, Frank says.
About six years ago, the Air Force grounded its fleet of C-130 cargo planes because of faulty wing bolts. Frank’s shop made the new bolts that enabled the badly needed planes to resume flying.
The innovations have continued, often along the lines of what Frank calls “the napkin design process.”
Creative ideas come to the team regardless of time or place so they’ll pull out a pen or pencil and draw on whatever they have.
About six months ago, the shop improved upon the laborious process of painting landing gear wheels. Staff Sgts. Alex Aguayo and Michael Rogers built a mounting stand that allows workers to paint the entire wheel at once, eliminating 13 hours of cure time and the cost of respirators and other materials that went with it.
The system is now being picked up by other bases.